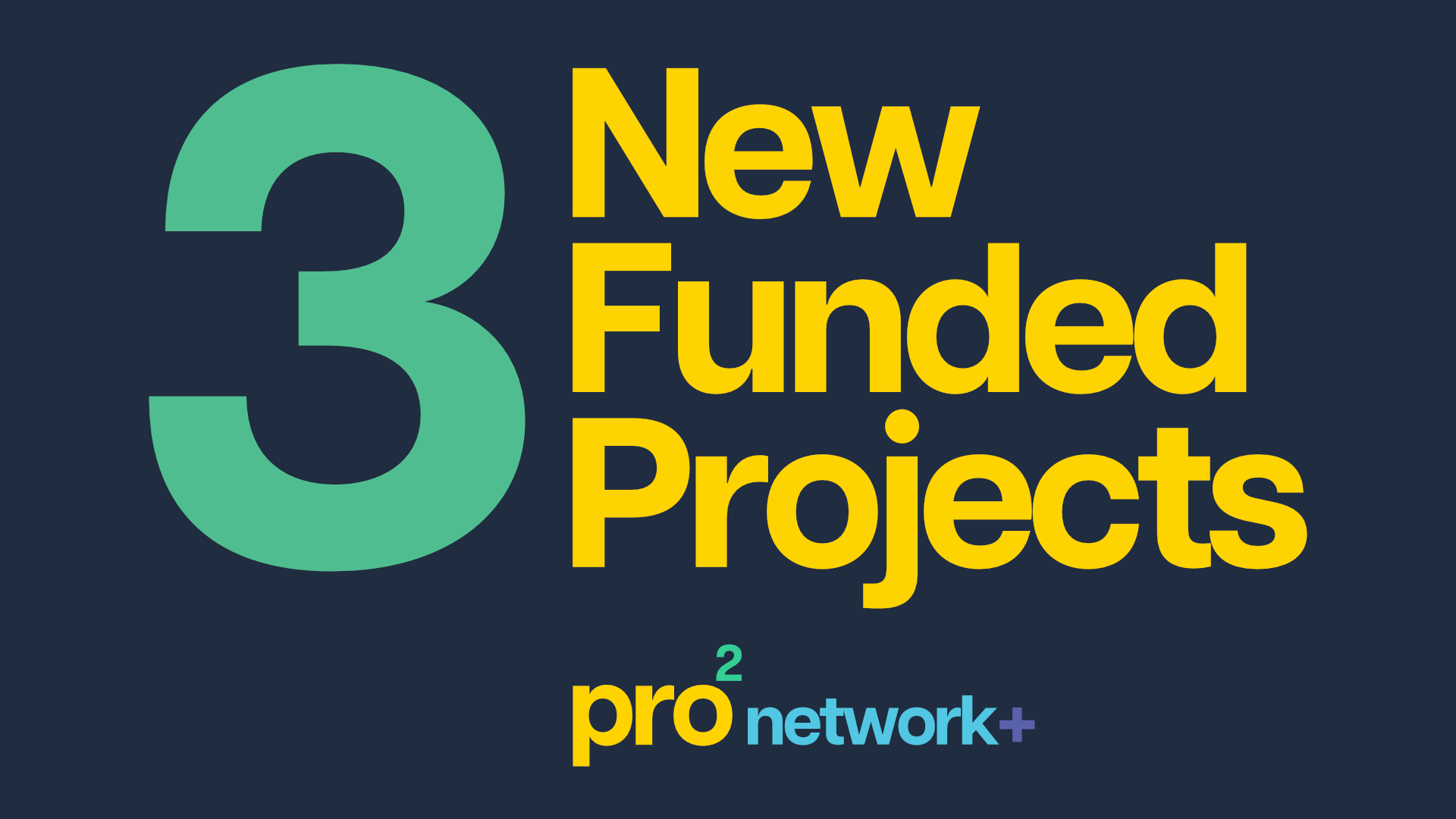
As creators of conventional electronics seek to refine and scale products, they encounter increasing complexity around collaborations with stakeholders, requiring a host of techniques, standards, and tools that can facilitate interactions across disciplines. This is where infrastructure for digital device production has a role to play in facilitating these interactions to empower more creators to produce devices at scale.
Last spring, the pro² network+ put out a call for projects relating to infrastructure to support digital device production that goes beyond traditional manufacturing, with a total of £240,000 in funding available. This might include leveraging technologies like the Internet of Things, artificial intelligence, and XR (including virtual and augmented reality).
We’re excited to announce that three projects were successful in their bid for funding. Launching this September, they aim to provide innovative solutions to the infrastructure challenge.
Integrating Quality Control Documentation into the Open-Source Hardware Design Workflow
There are now a wide range of open hardware projects available which provide creators with the required instructions for replication, making it possible for people all over the world to produce their own devices. However, these instructions lack provisions for design improvement and record keeping that enable quality auditing.
This project seeks to provide a model solution in which quality checks and data capture are integrated into the assembly instructions for the OpenFlexure Microscope, an open source digital microscope developed by the project team. The microscope has already been replicated and put to use in over 50 countries, with its success owing mainly to its high-quality documentation so that assembly is reliable and components easily sourced locally. By enabling people to provide detailed feedback and facilitating better record keeping, the project aims to overcome challenges presented by a lack of quality checks. Overcoming this barrier will lead to the development of a quality assurance/quality control toolkit, to be integrated into hardware assembly instructions and progressing the OpenFlexure Microscope from small scale production to the sales of kits and assembled microscopes.
The project is led by Dr Richard Bowman, a Royal Society University Research Fellow in Physics and Astronomy at the University of Glasgow. He’s joined by team members Julian Stirling, a Freelance Consultant based in Bath, and industry partner IO Rodeo, an open science hardware design and manufacturing company in California.
Conversational Prototyping: Leveraging generative AI to support iterative device production and testing
Artificial Intelligence (AI) systems based on Large Language Models (LLMs) are rapidly becoming a tool that many people rely on for daily tasks in both the home and the workplace. Models like ChatGPT can aid with everything from writing emails to scheduling dinner parties, and they are already being used in prototyping electronic devices, particularly when it comes to writing code.
Developing hardware can be more complex, however, especially when making use of things like sensors and actuators. Iterating for small or large scale production can require considerable time and resources. This project seeks to overcome this challenge by leveraging the power of LLMs through a novel approach called ‘Conversational Prototyping’. It would allow developers and end users to work in conversation with an AI system to develop the functionality of a prototype, incorporating sensing and actuation.
The project aims to produce three primary outcomes: a physical testbed that connects an LLM with sensors and actuators; a set of prompts and commands guiding the LLMs interaction with the testbed; and an evaluation of this approach to prototyping. Leading the project is Professor of Design and Innovation at Nottingham Trent University, Lars Erik Holmquist, who also heads the Connected Experiences Lab. He’s supported by two industry partners, Datalink Electronics, a contract electronics manufacturing company from Loughborough, and Electric Circus, a Netherlands-based artistic collaboration which implements robotics to explore new approaches to puppetry for use in street theatre. Also assisting the project is Poppe & Partners, a company specialising in the combination of culture and technology.
Multi-modal XR prototypes for stakeholder interactions and testing
University of Bristol Senior Lecturer in Engineering Design, Chris Snider, leads this project which seeks to improve the way stakeholders like clients and end users feedback on device prototypes. During the ‘isotyping’ process preliminary versions of the design are produced and refined – known as isotypes – for development, testing, and user evaluation.
To receive quality feedback from stakeholders, it’s best to present them with designs as close to the final version as possible. Unfortunately, such isotypes are extremely costly and typically can’t be produced until late in the process – even beyond the point where changes are viable to make.
Instead, designers have to rely on sharing partial representations or even just pictures. These hamper stakeholder understanding of the product and whether it will meet their needs, and limit their ability to provide clear feedback. Issues arising from poor stakeholder interactions can lead to significant delays and costs, sometimes even impacting the viability of a product when producing devices in low-volumes.
To solve this problem, the project aims to leverage XR (augmented, virtual, and mixed reality) technology to empower stakeholders to experience a detailed and accessible isotype at a much earlier stage than previously possible. Tangible physical interactables would be paired with digital models in a 3D space, allowing for realistic product interactions overlaid with digital aesthetics. Packaged as just an XR headset, app, and minimal set of hardware, it would integrate active and passive feedback capture systems to communicate detailed information back to developers and allow for remote evaluation and collaboration with global stakeholders at low cost.
Kinneir Dufort, a design and product development consultancy specialising in healthcare, are supporting the project alongside University of Bristol Research Engineers Aman Kukreja and Chris Cox.’
What’s next?
If you’re curious to know more about these projects, follow us on LinkedIn, X, and Instagram for updates. You can also register for free to be a pro2 network+ member, giving you access to the member’s section of our website for networking and collaboration. Members also receive the pro² newsletter with information about our events, future funding calls, and everything we’re doing to democratise the production of digital devices.